
These are instructions for the DIYer on how to remove the H/F series balance shafts for under $20.
It is assumed that anyone attempting this has some experience with drilling/tapping aluminum and freeze plug and bearing removal and installation.
Parts:
(1) 12 x 20 m6* Dowel
(3) 10 x 16 m6* Dowel
(1) 40mm Freeze Plug
(1) 1" Freeze Plug
(1) 1/8" NPT plug
(3) 5/16-18 set screws
Loctite
Permatex sealant
Tools:
- Hammer
- Dremel with Pencil attachment
- Punch
- Tap set
- Drill bit set (fraction and letter)
- Press (optional)
*"m6" is the spec for how tight a dowel pin fits inside of the hole. m6 is tight but removable, perfect IMO.
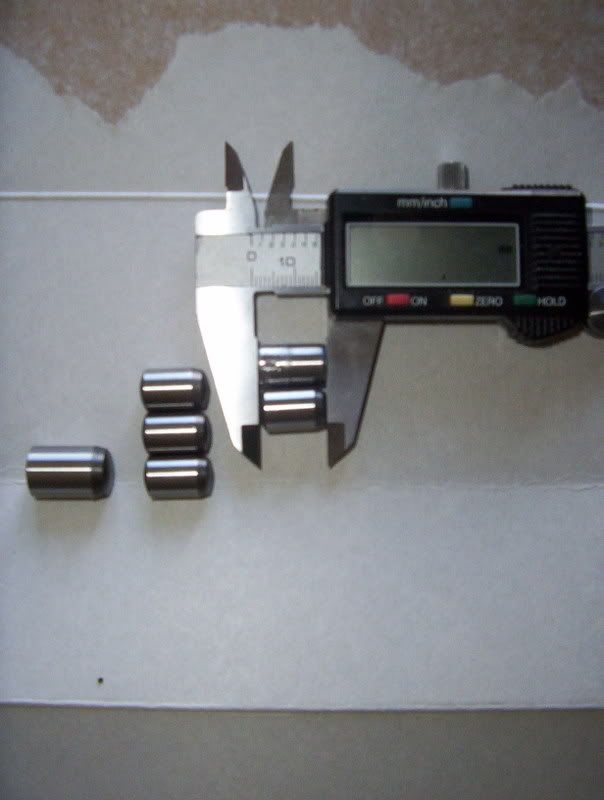
I purchased these dowel pins at a local supply store that specializes in fasteners. At first glance they look shorter than the hollow Honda OEM dowel pins but they are in fact the exact same height. Note that one end is tapered.
1/8" npt plug.
<FONT SIZE="4">Rear Balance Shaft</FONT>
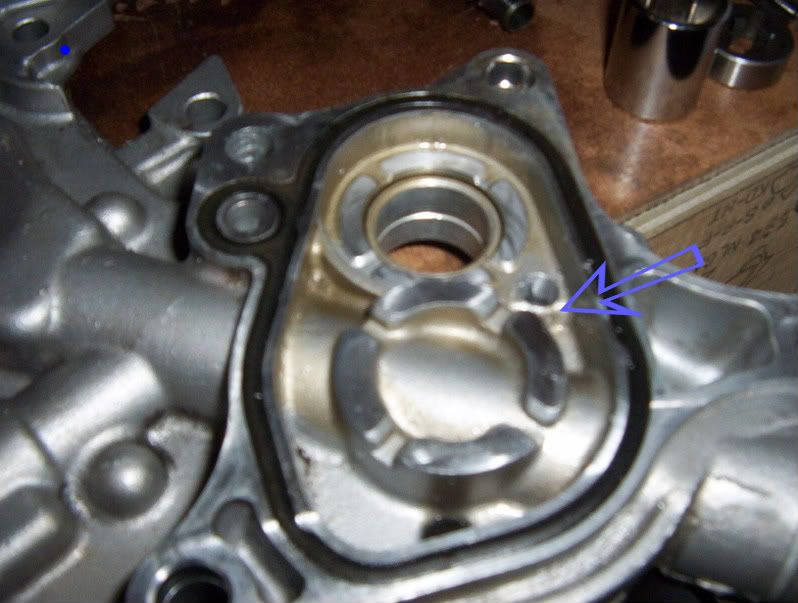
My experience tells me that this small piece of aluminum should be ground off before drilling and tapping this hole. Otherwise there is a good chance that this will crack off when you tap this hole.
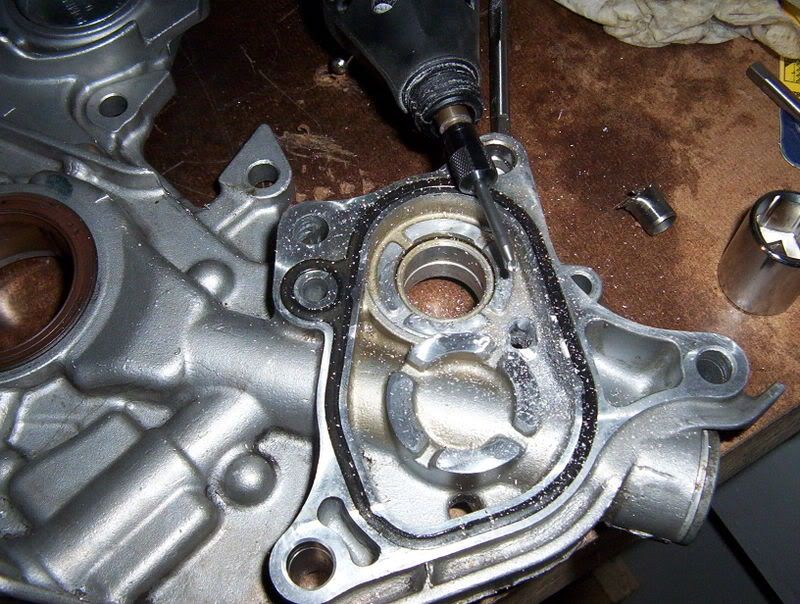
2-3 minutes of careful grinding and this hole is ready to be drilled.
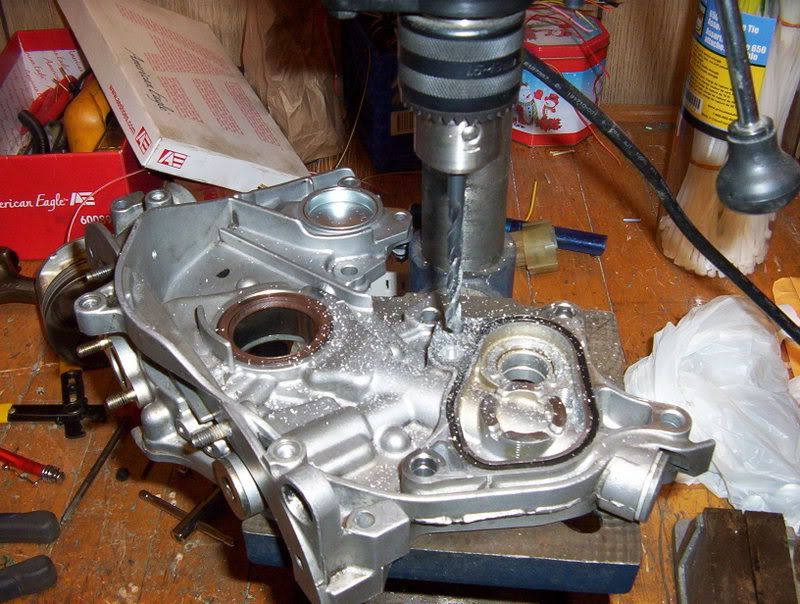
An "F" drill bit is ideal for a 5/16-18 tap
Dill holes as required.
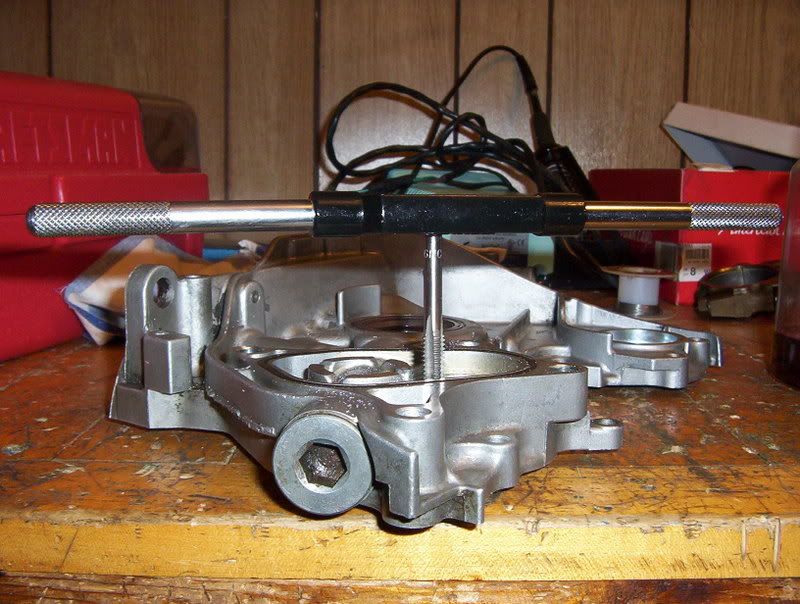
<FONT COLOR="Red">Since (non-tapered) set screws are being used it is a good idea not to tap all the way through the holes. This allows you to tighten the screws.</FONT> It took me a couple of tries on each hole to get the holes deep enough.
Clean holes and install set screws using an appropriate amount of sealant. I used black permatex sealant.
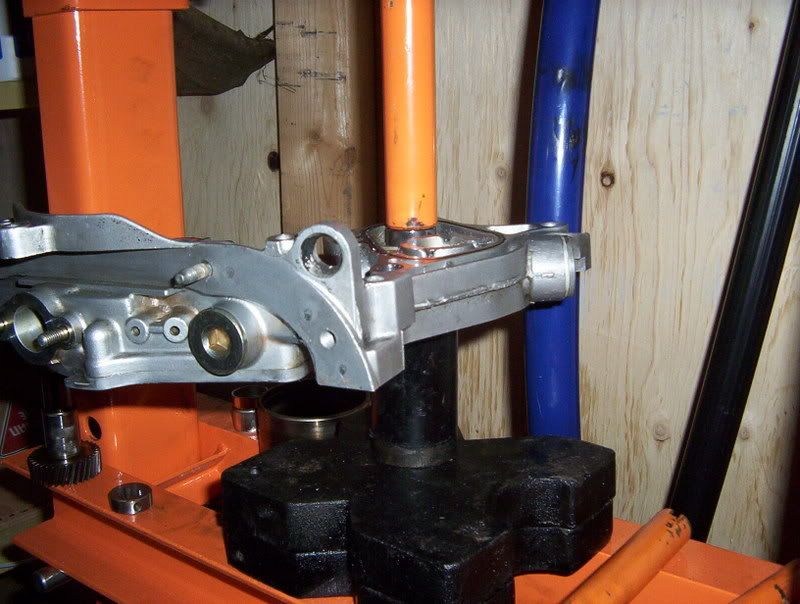
- Press out Bearing. The pictures shows an appropriately sized socked pressing out the bearing.
- Install 1" plug flush with the oil pump using your sealant of choice. Don't worry about the oil hole on the other side of the plug.
<FONT SIZE="4">
Front Balance Shaft (Oil Pump Assembly)</FONT>
oil pump pic
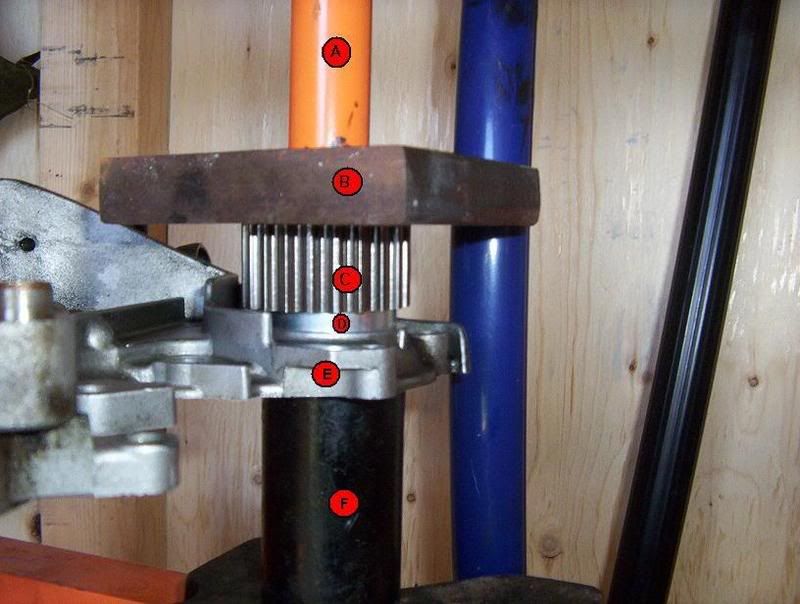
A - Harbor Freight press (which BTW can be purchased with the money you save not buying an expensive balance shaft removal kit)
B - Chunk of metal
C- One of the balance shaft gears (works prefect!)
D - 40mm Freeze Plug
E - Oil Pump Assembly
F - Perfectly sized 32mm impact socket
This is the point you realized that you forgot to put loctite/sealant on the 40mm freeze plug. Take this all apart, clean hole, apply loctite, re-assemble and press in the freeze plug as required.
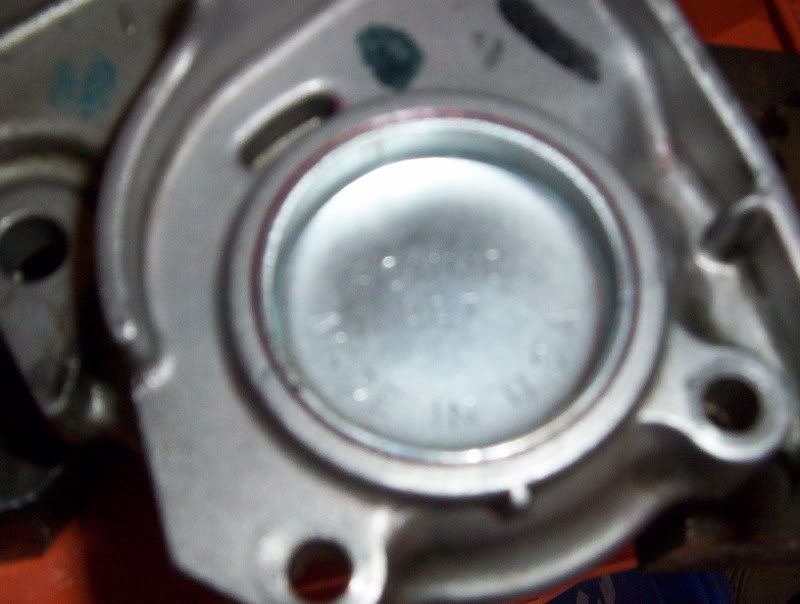
40mm "Made in the USA" freeze plug installed; save money on your balance shaft removal and support the American economy.
<FONT SIZE="4">Removing Bearing</FONT>
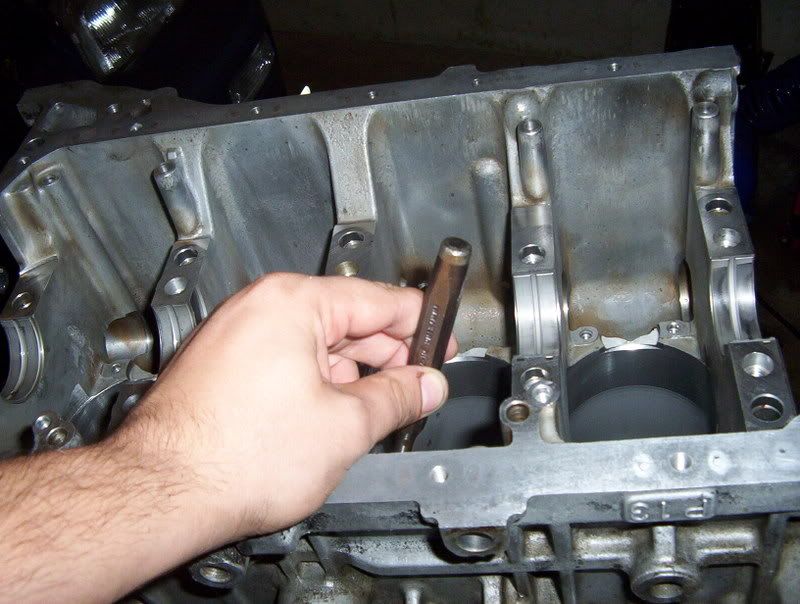
Don't have a cam bearing removal tool? There's an easier way!
The first thing I did was give the bearings tab a decent beating.. My first intention was to beat it out of there but that didn't quite work. Bending the tab down did however help later on in the process.
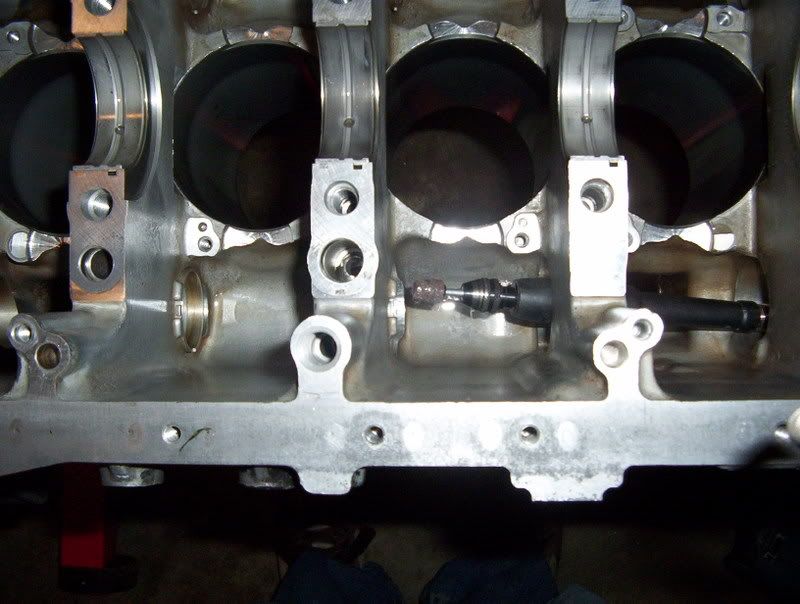
Using a dremel pencil attachment and a grinding stone I cut a slot into the bearing. (bearing not pictured) No need to get emotional about nicking the aluminum.
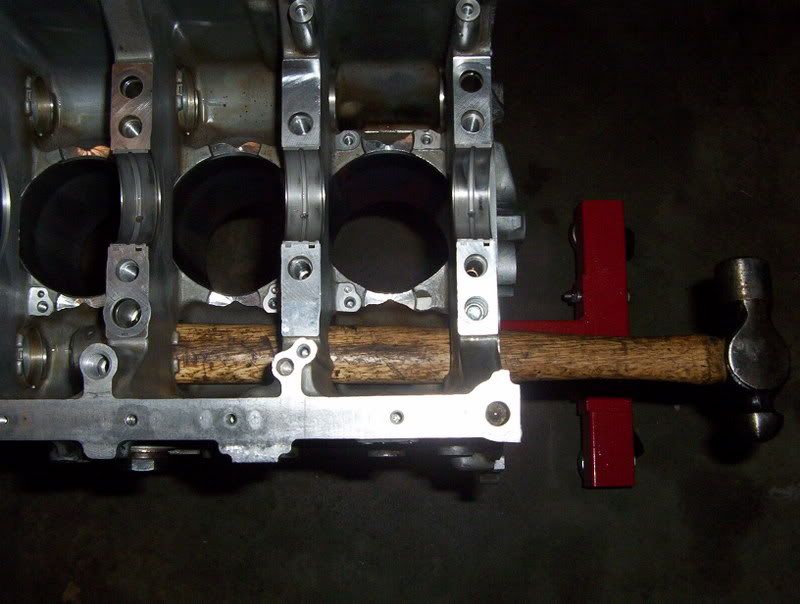
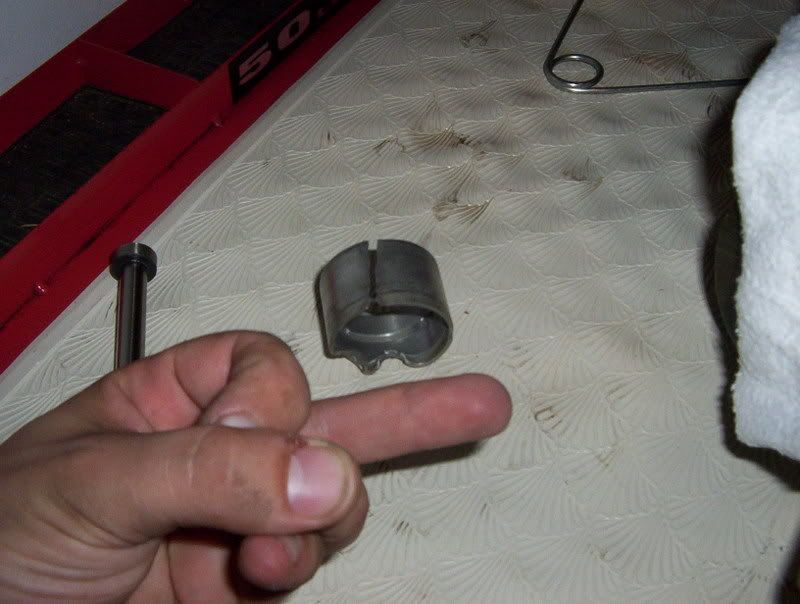
A few light taps with a hammers handle on the bent bearing tab and the bearing is out.
<FONT SIZE="4">Tapping Oil Hole</FONT>
A dowel will not work for this hole, a tapped hole with an 1/8" npt plug works perfect.
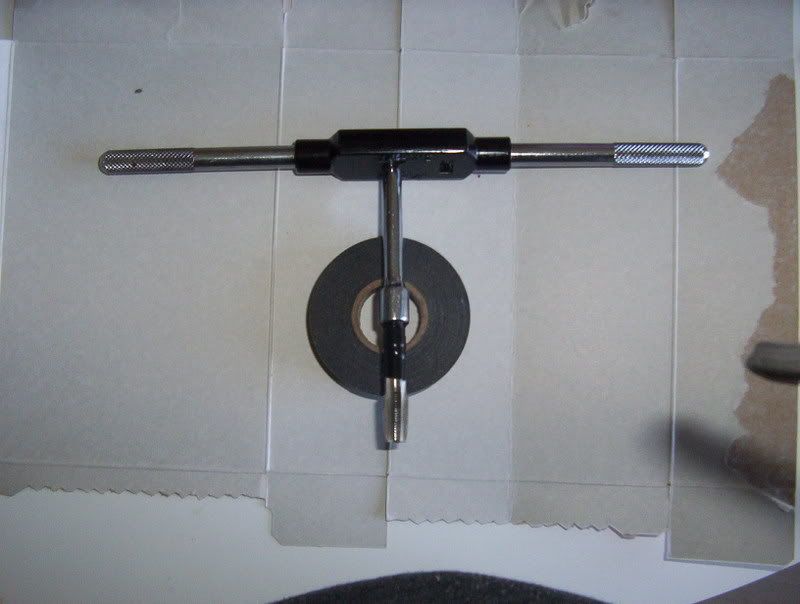
Tap not long enough? Use a 1/4" extension with a tiny bit of electrical or pipe tape around the tap. This of course only works with taps with a small shank. If anyone has a better way to do this please speak up.
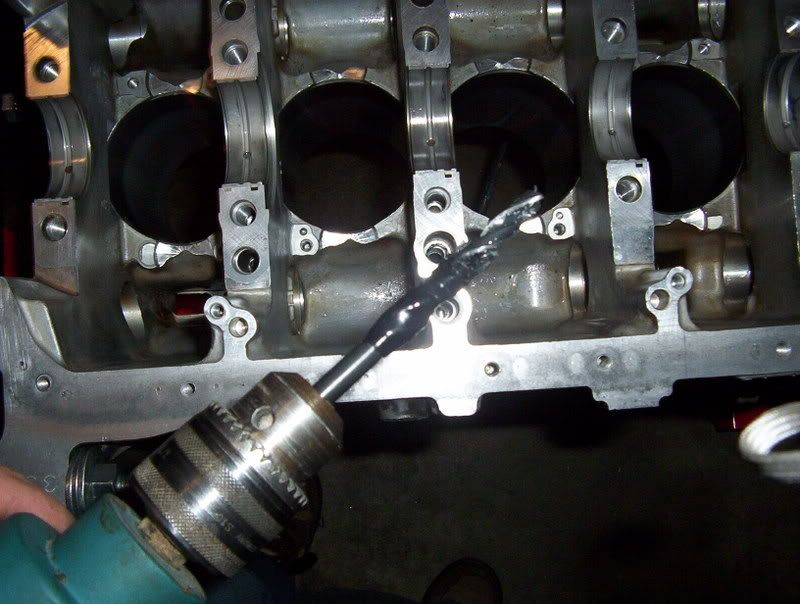
21/64" bit with some electrical tape in case of a slip. Aluminum likes to grab drill bits when you have a pre-drilled hole so hold on tight.
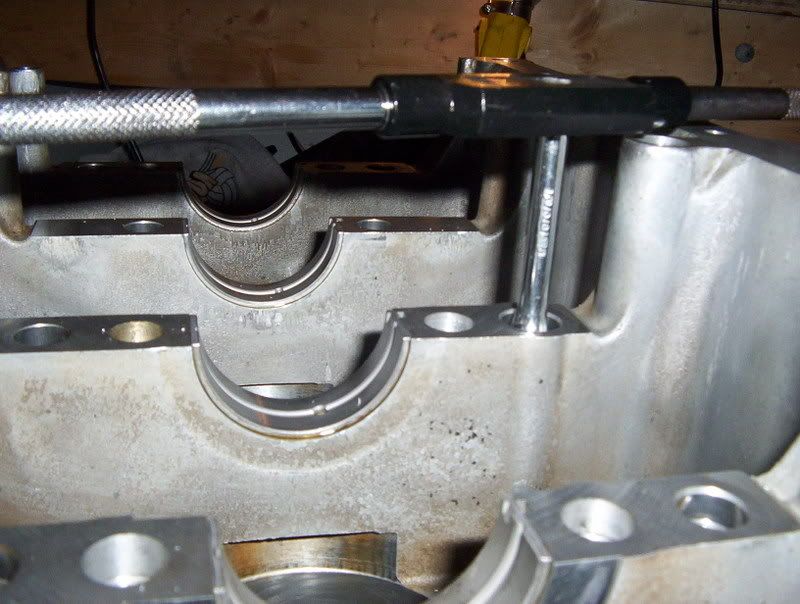
If you don't have experience tapping aluminum now is not the time to learn. You've been warned.
I had to go pretty deep with this particular npt tap to get the plug slightly counter-sunk. Took a couple of test fits before I got it just right.
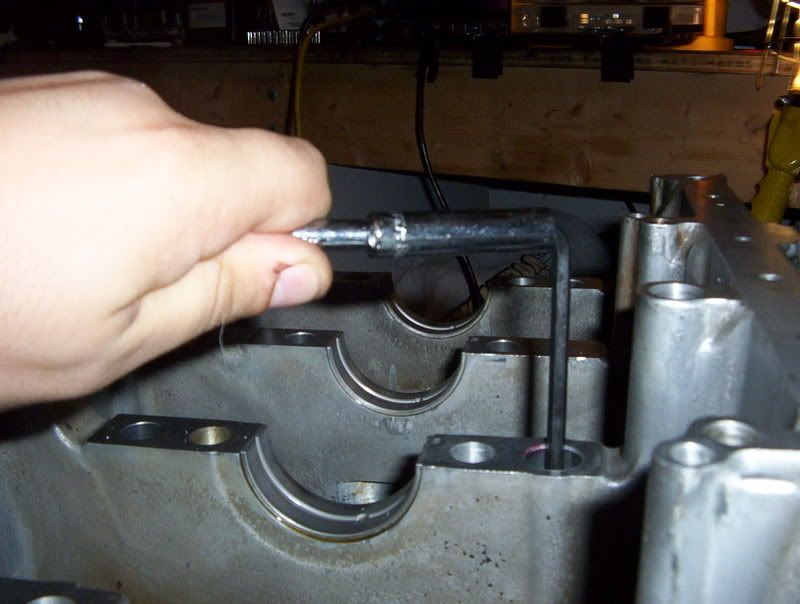
A dab of red loctite and a half-turn with a small pipe (after finger tight) and this hole is plugged!
<FONT SIZE="4">Plugging oil holes</FONT>

Main caps 1,3 and 4 pictured. The solid dowel pins are plugging the oil holes to the balance shafts]. I chose to tap the dowels in to the main caps with the tapered side sticking out. This was a bit tricky and took some time.
There is around .100" sticking out for location purposes. This is enough in my opinion but you can always step up to a longer dowel if it makes you feel better.
-----
have anyone done this? and is there anything else i need to know to do it?

original post
http://honda-tech.com/all-motor-natural ... l-2391818/