I continued to drill roughly within my outline...
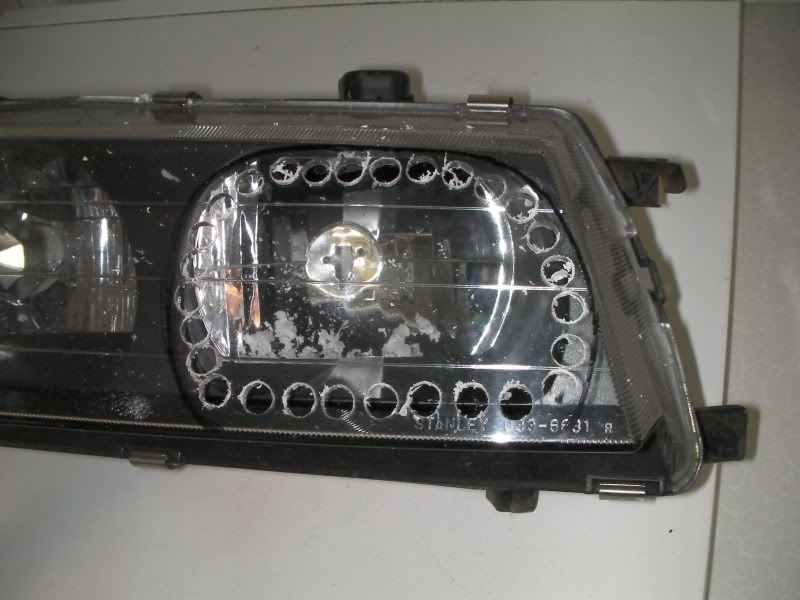
Which then enabled me to make short work of using a junior hacksaw blade to cut it out completely...
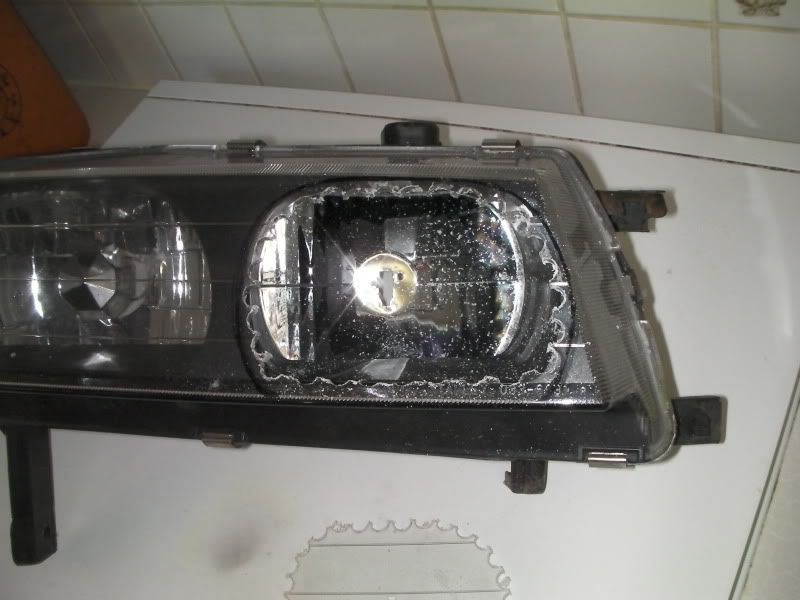
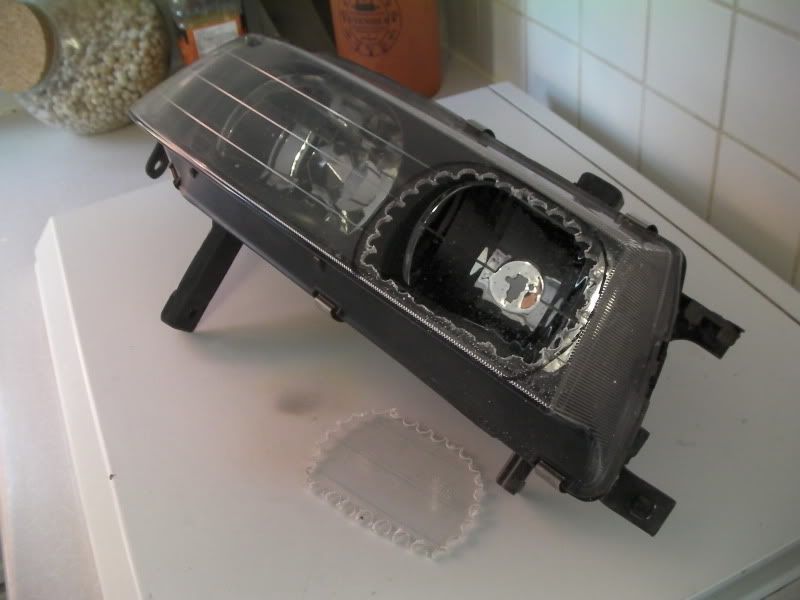
Then in order to remove the actual mainbeam reflector I needed to unfix the assembly brackets on both sides of it...
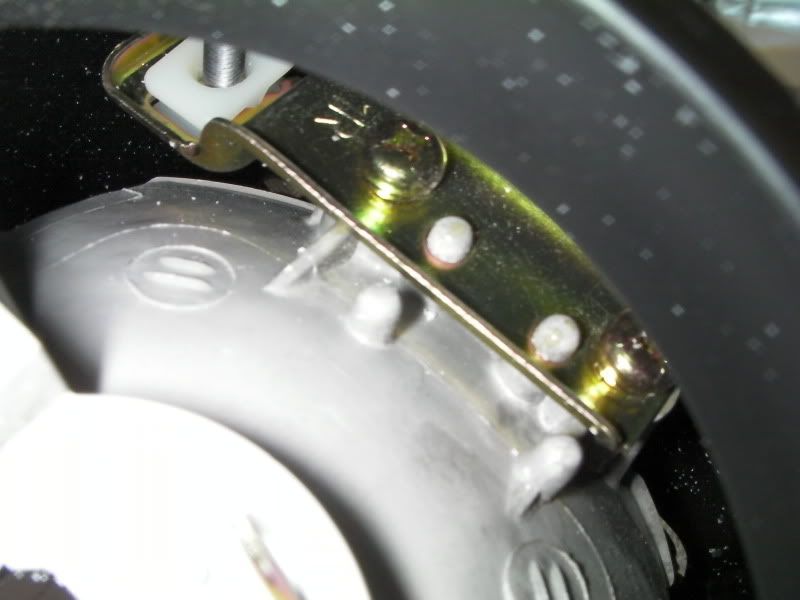
Now it's impossible to actually get a screwdriver in there, so I simply drilled 4 holes above each screw...
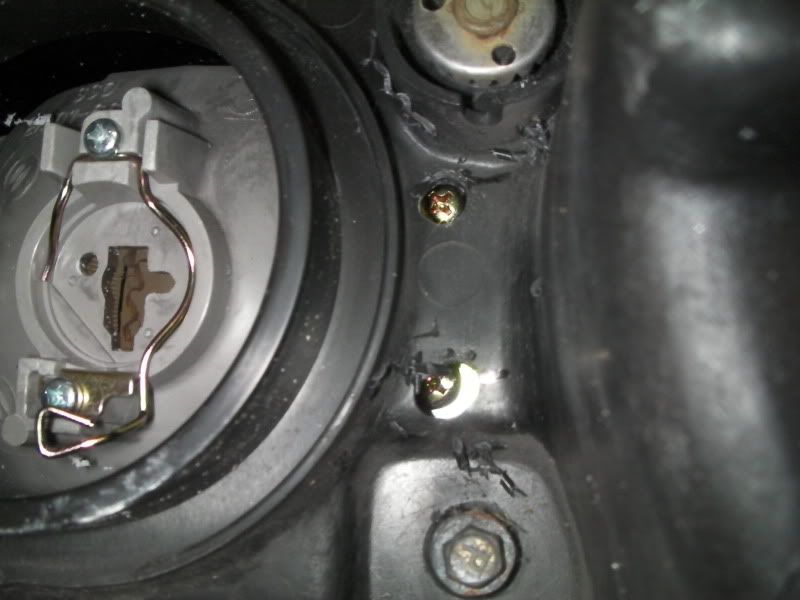
Then with the reflector loose inside the headlight I literally took my clobbering screwdriver and hammer to it...
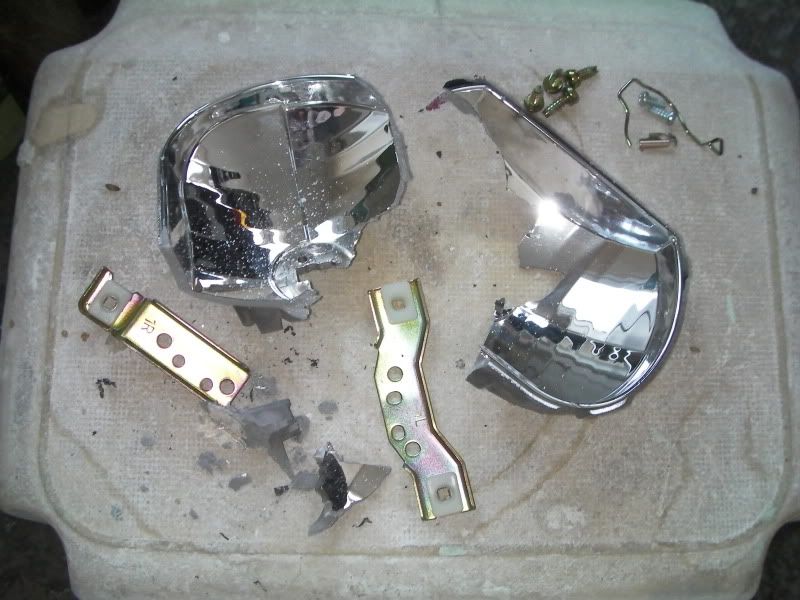
Now I can see exactly what I'm dealing with...
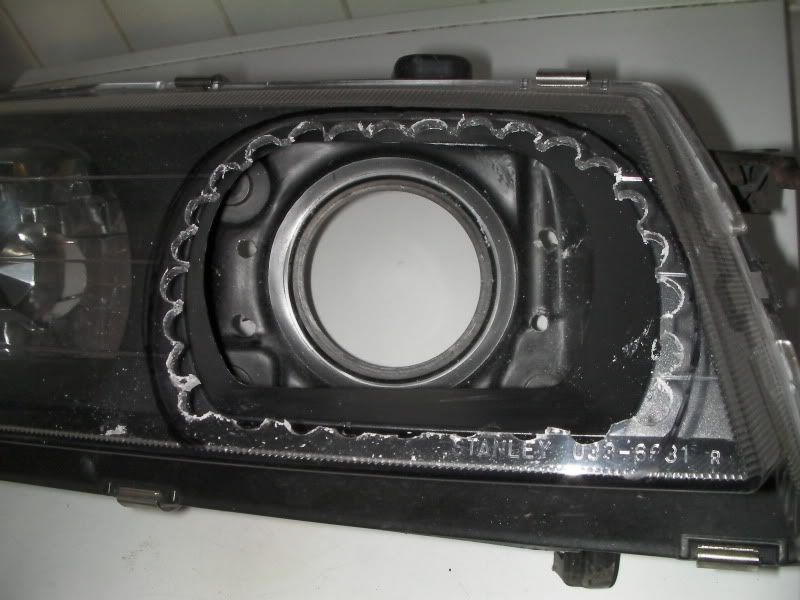
I'll obviously need to fill in those 4 small holes again...
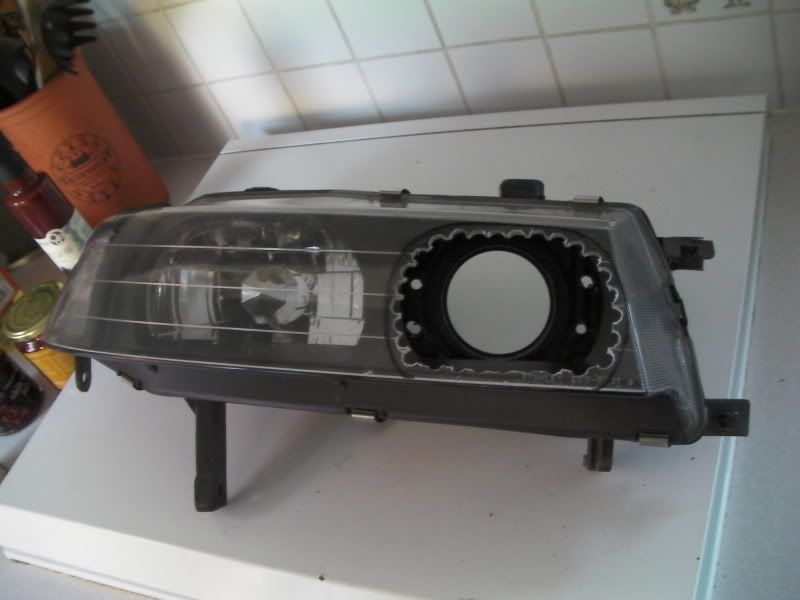
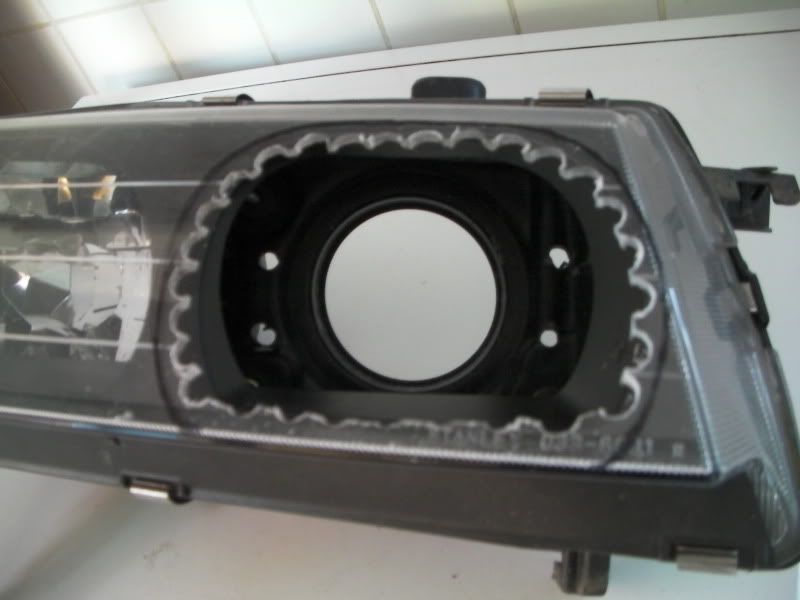
The adjustment screws I'll probably leave as they're not in the way...
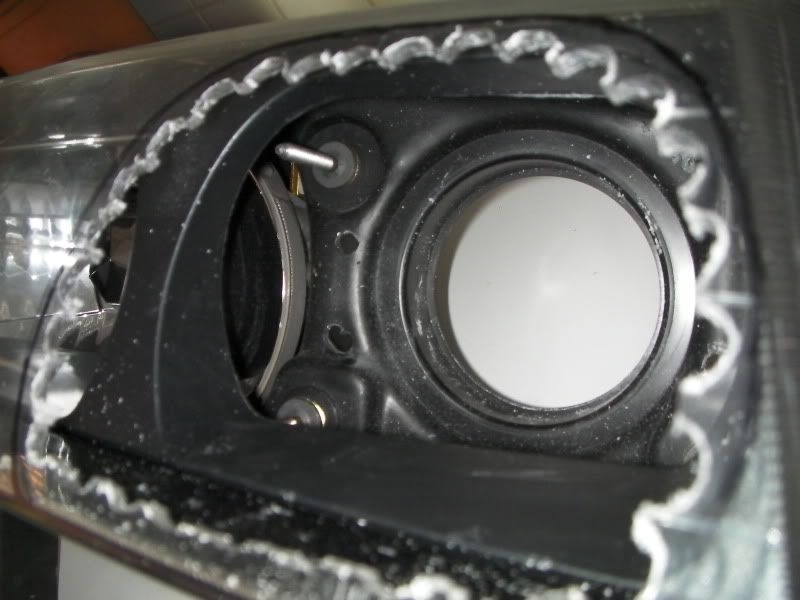
I then used my grinding stone and drill to grind away the lense up to my marked line...
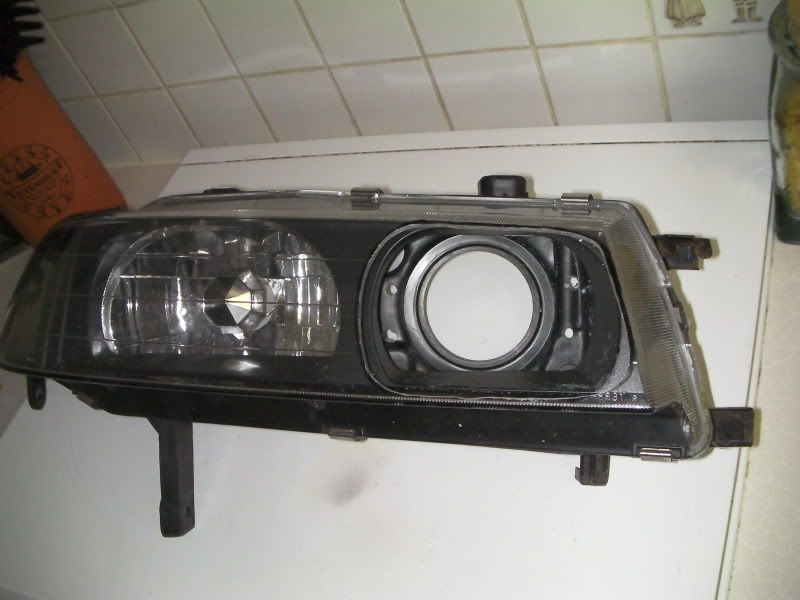
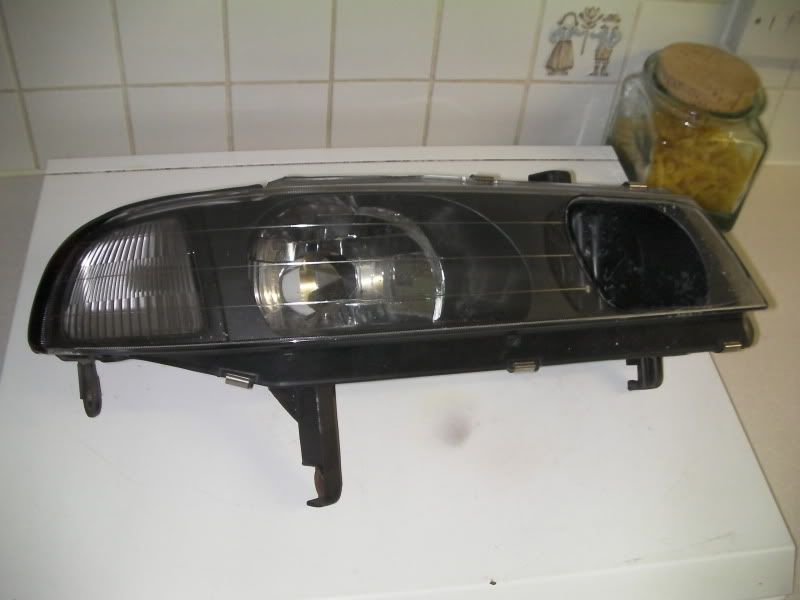
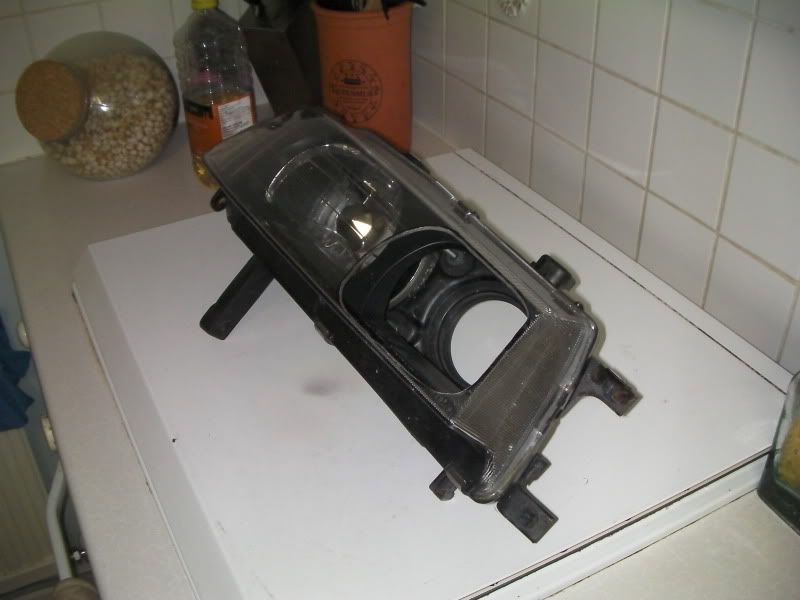
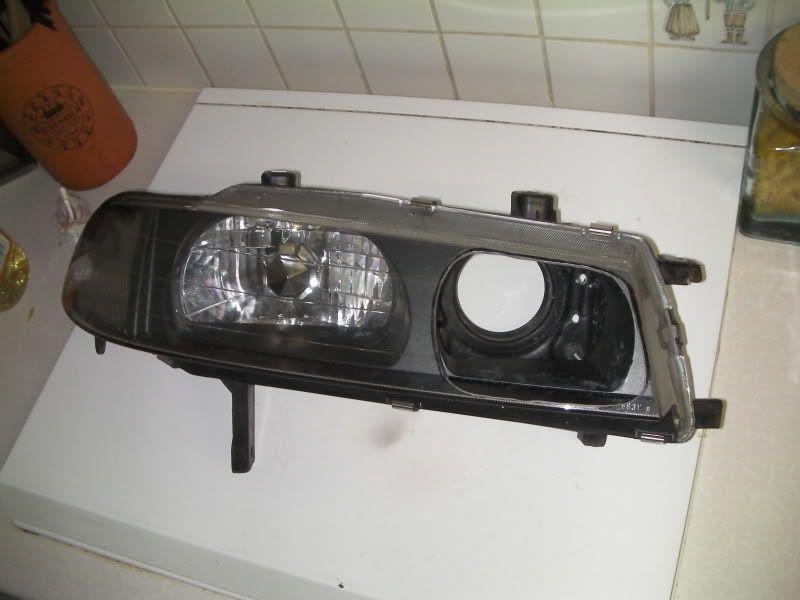
It's only a rough edge which I can obviously wet & dry back smooth, but I think I'll end up covering the ede with a small lip anyway, so it's not an issue.
Then, as I stated before, the back of the headlight lends itself perfectly to connect a 3" silicone duct...

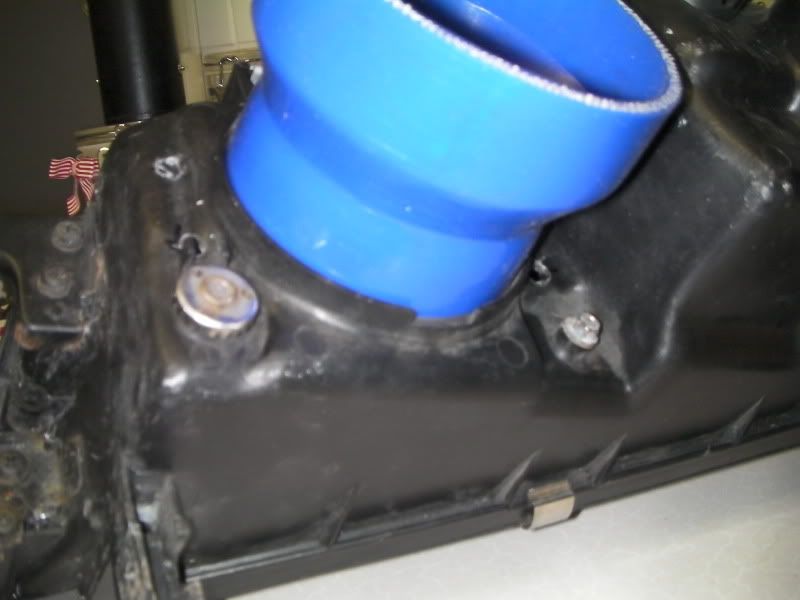
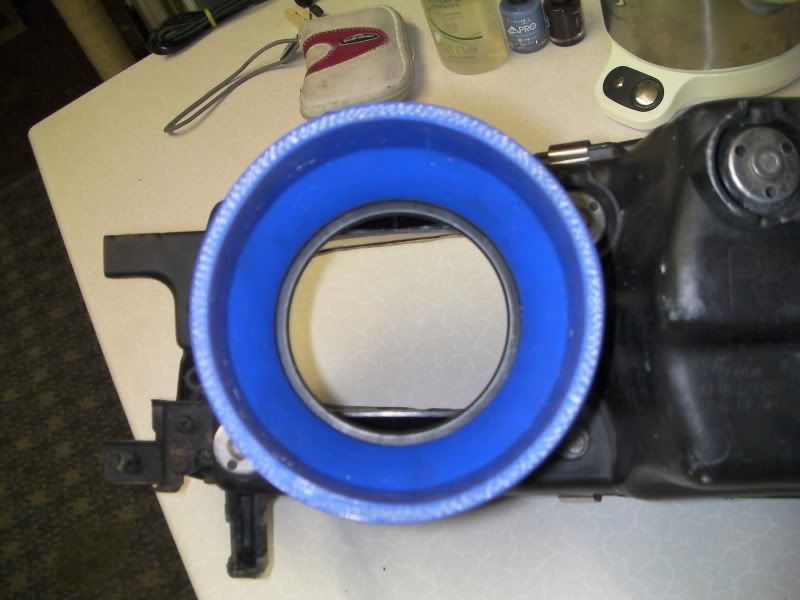
This silcone reducer is a 4"-3", which I had bought ages ago for another plan, but I thought it's ideal to now show you what I'm about to show you...
The next larger ring on the back of the headlight also leads itself perfectly for a 4" silicone duct connection...
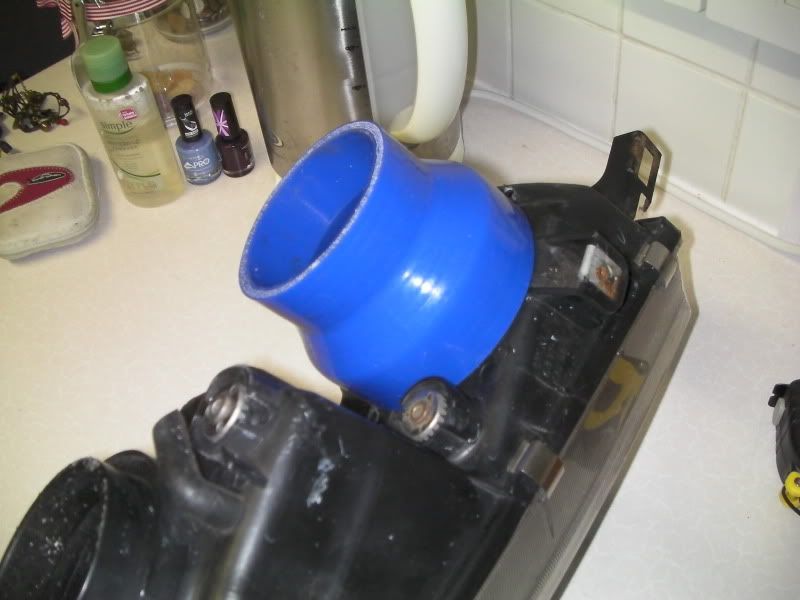
So I decided (as I had wanted to from the start, hence the 4"-3" reducer) to open the back of the headlight out to a 4" diameter feed. So again, I made the cutting easier by drilling around the ring...
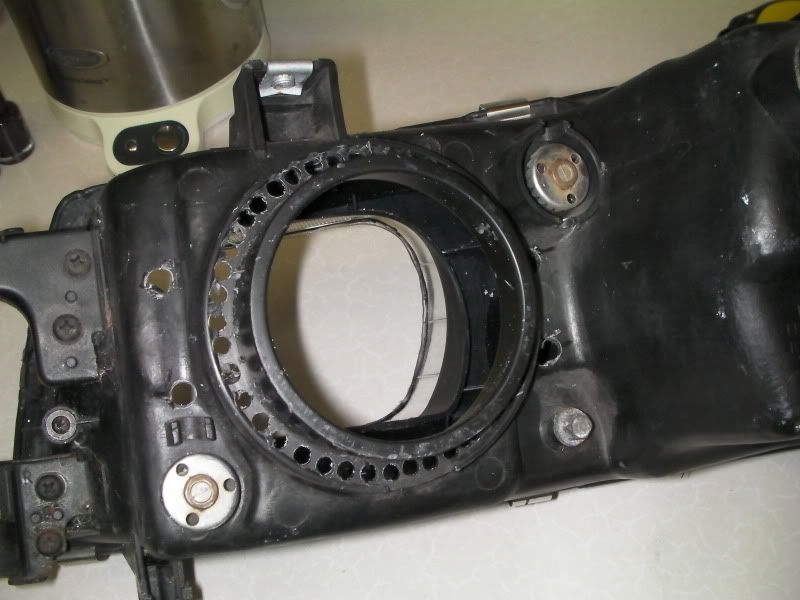
And then used a stanley knife to cut it out...
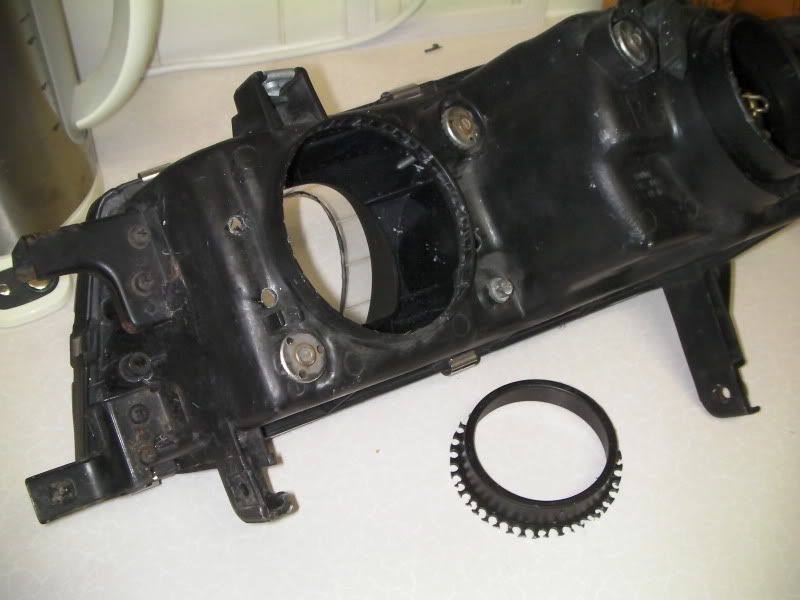
So now the through shot looks like this...
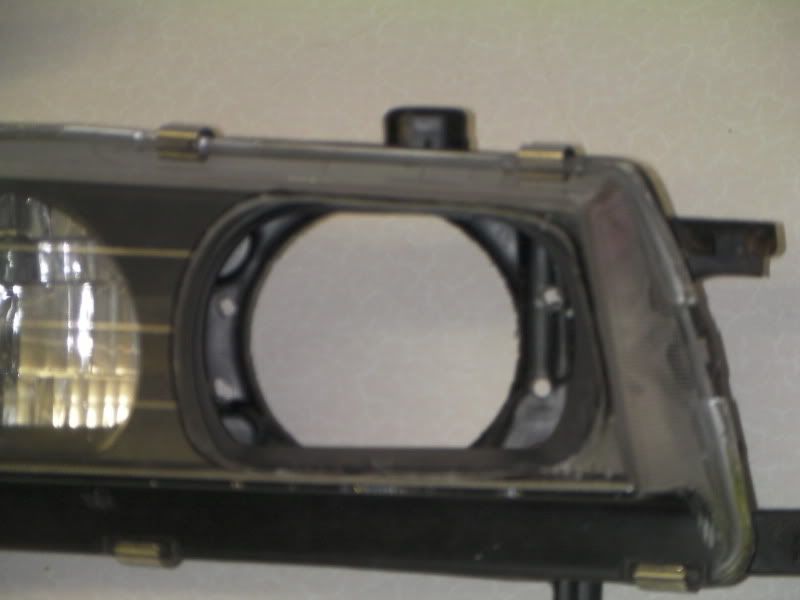
The next step is to create a template to create the feed walls and to enable me to reseal the headlight, so...
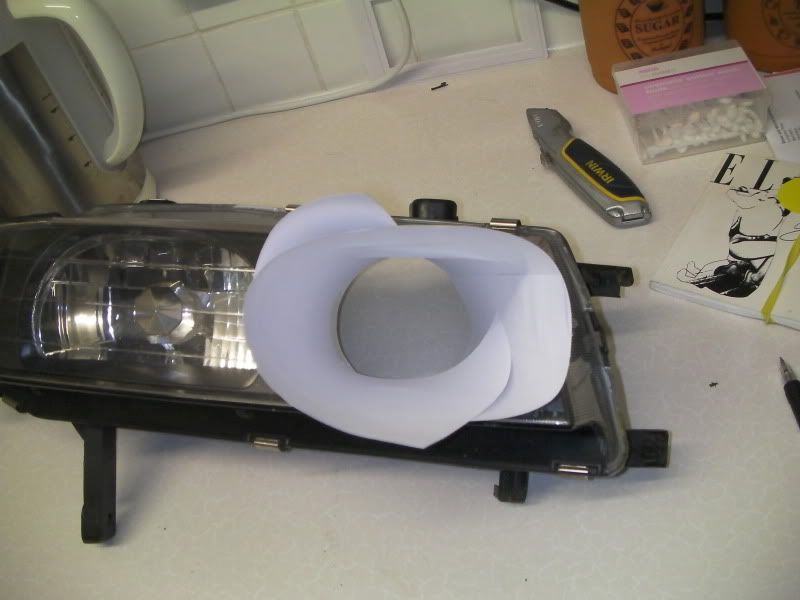
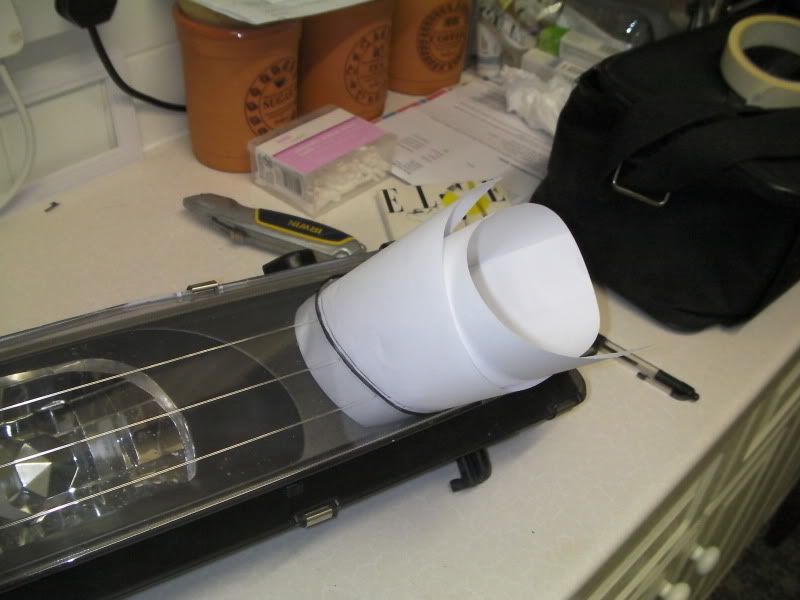
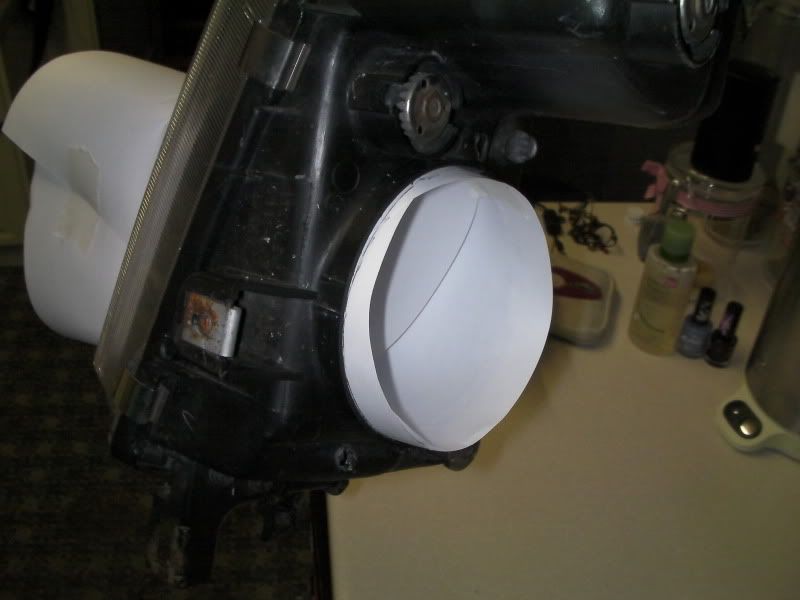
I simply unscrewed/expanded the paper roll until it met all of the edges of the lense and the back and then drew around it to cut it out. I then popped it back for a trial fit...
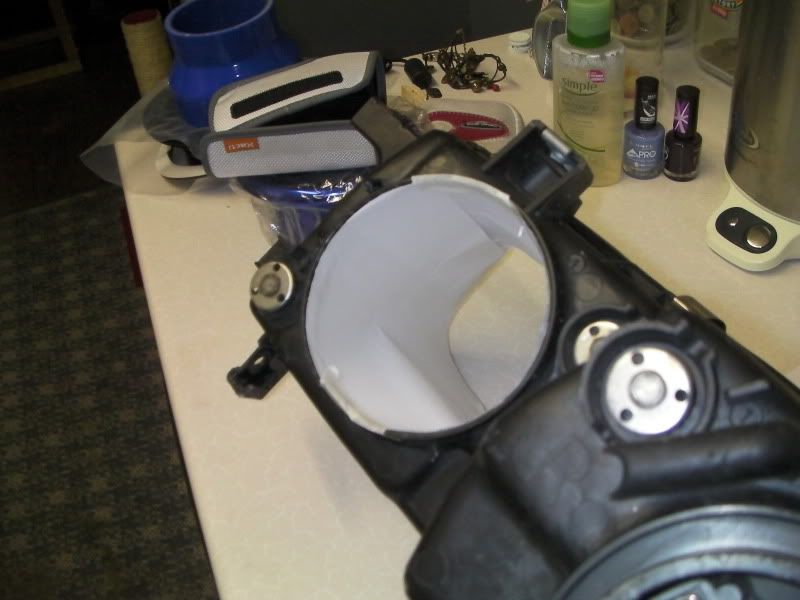
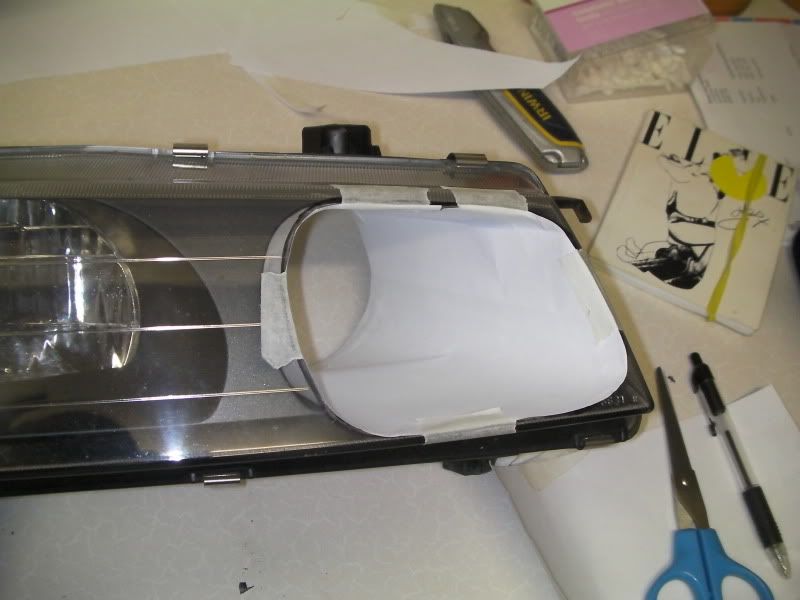
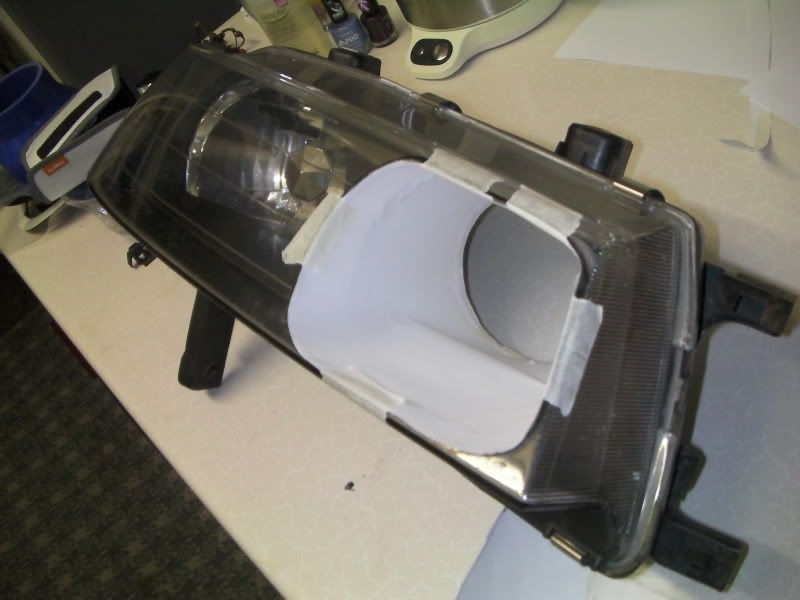
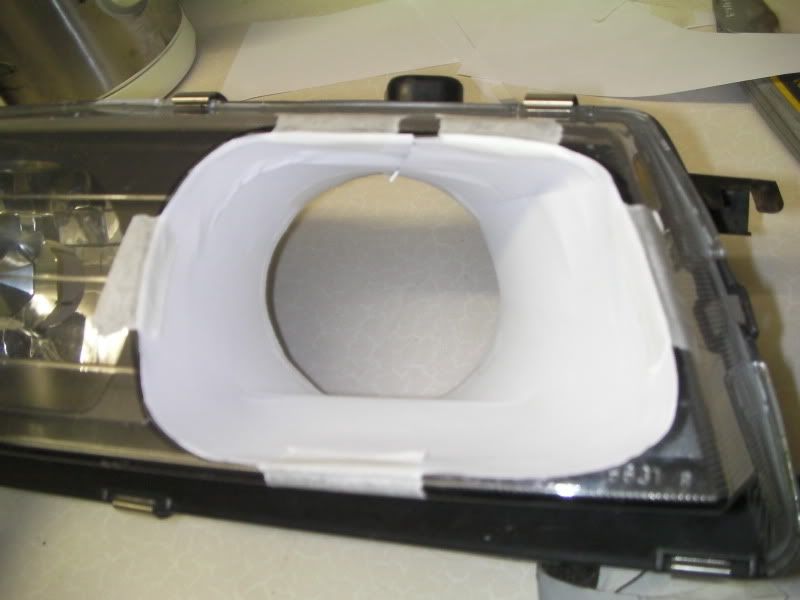
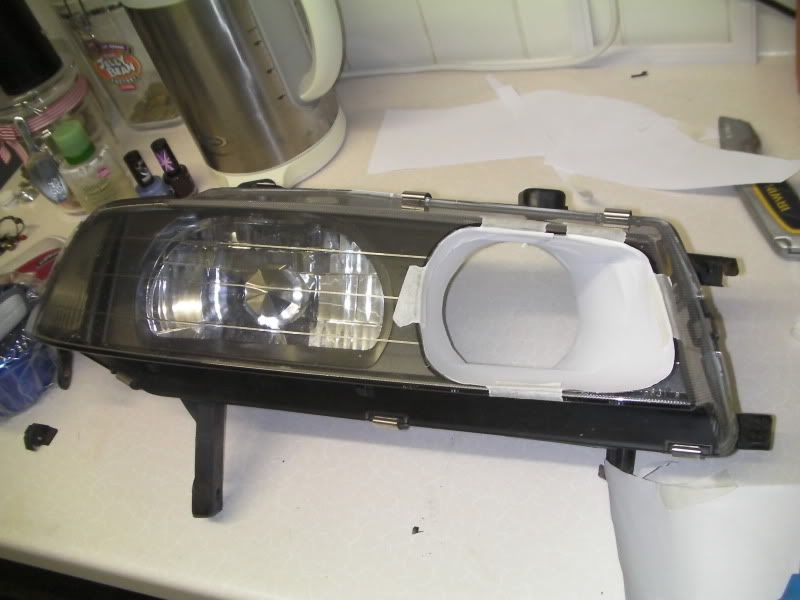
Looks good and will look better, so I have me a template!

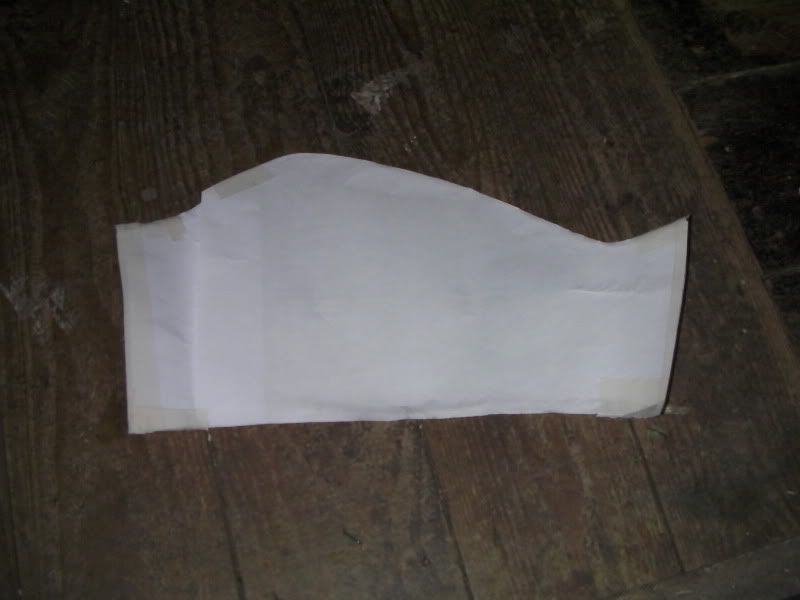
That's as far as I've got for now. Just need to decide what material I want to make the feed out of. Carbon Fibre would be nice, but I think far too fiddly and messy, so I'm thinking simply a thin gauge aluminium.
Then today I managed to finish cutting my hole in the bulkhead

I managed to pick up a new (more fit for purpose) hole cutter...

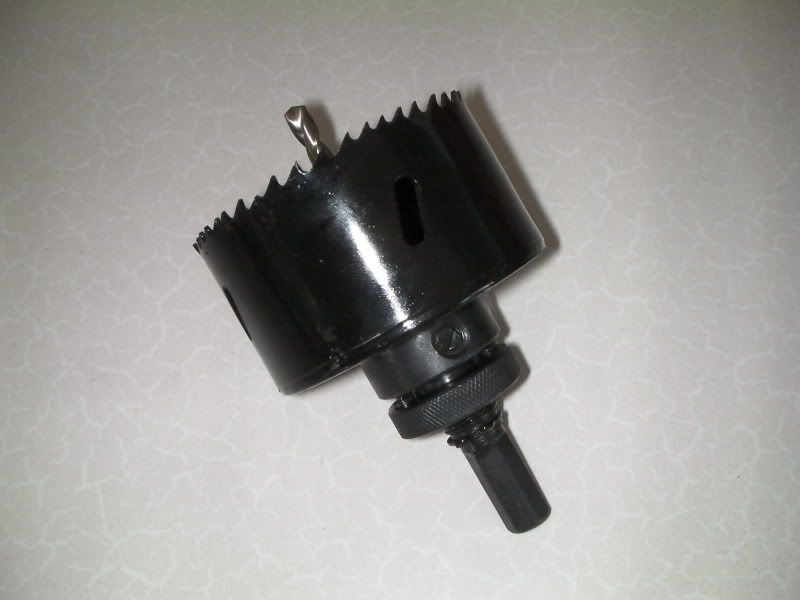
Which made relatively light work of the 2 ply bulkhead...
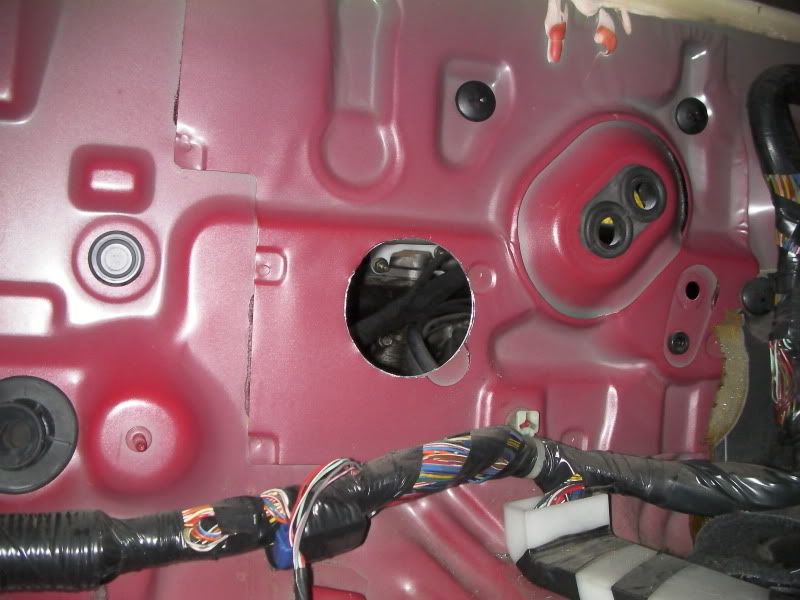
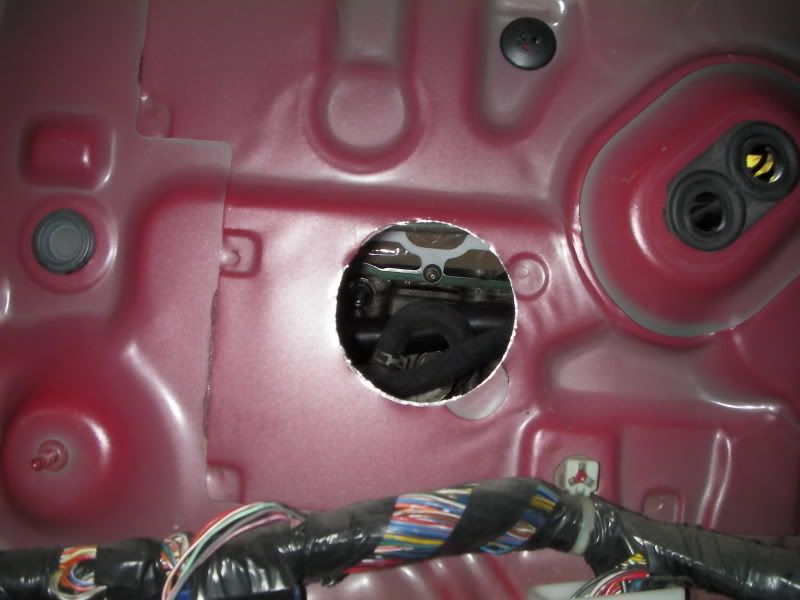
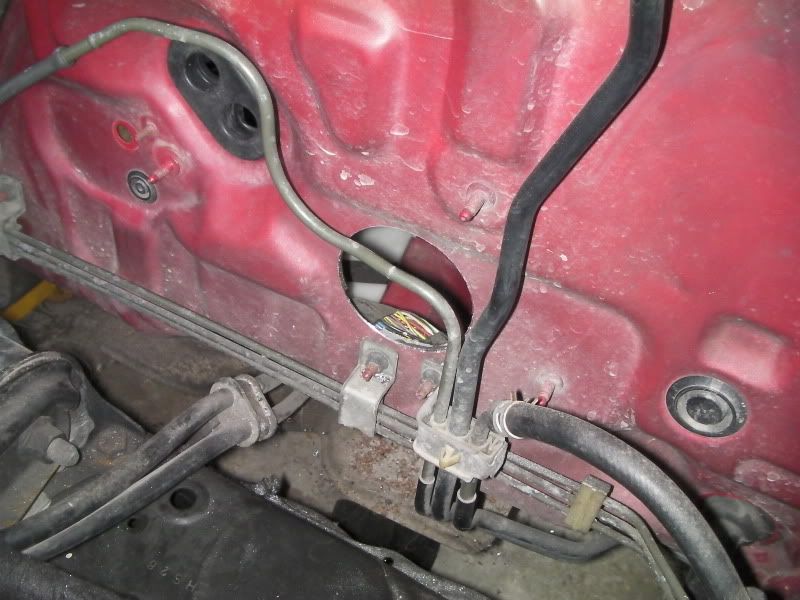
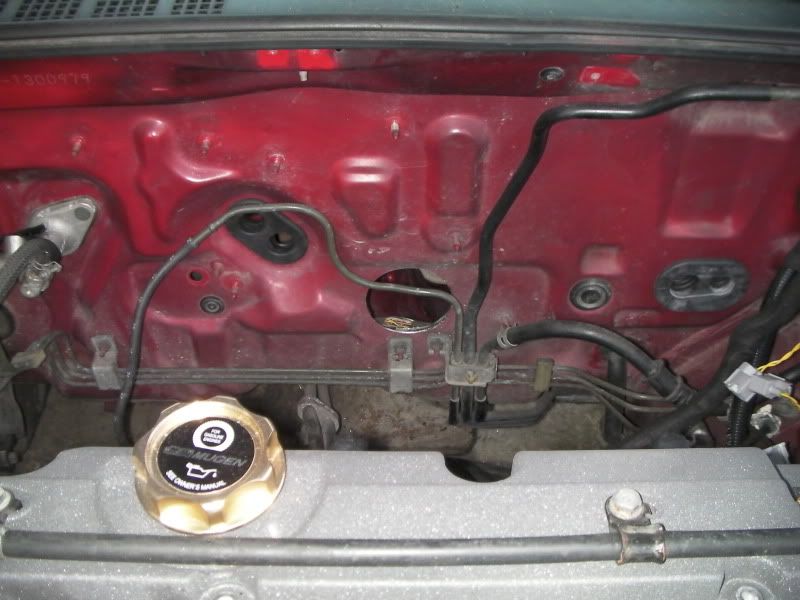
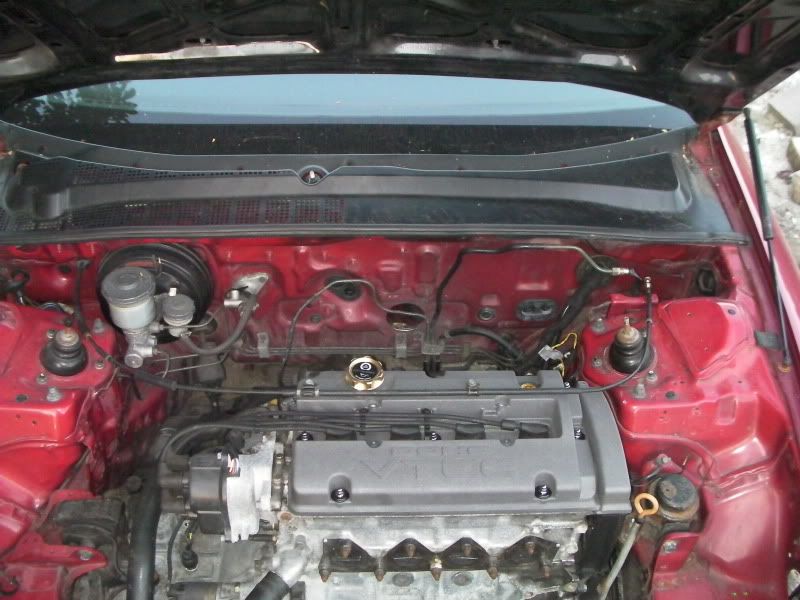
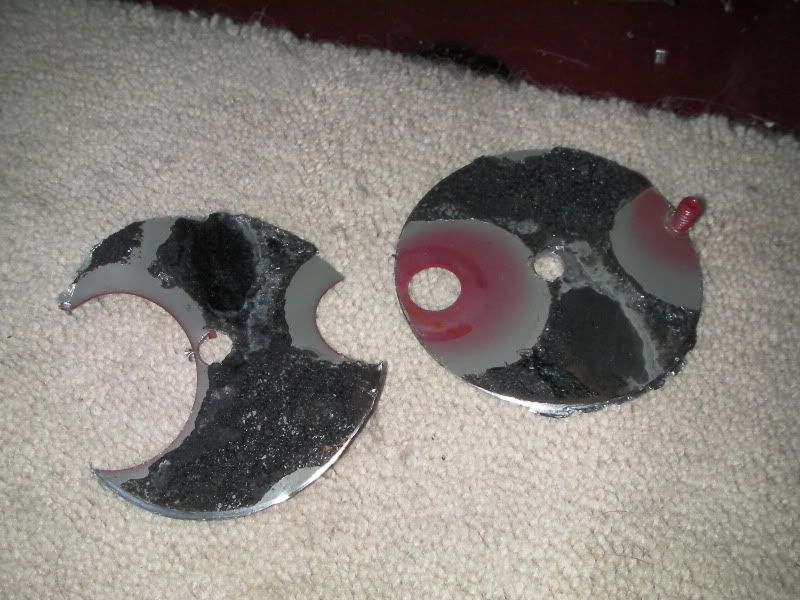
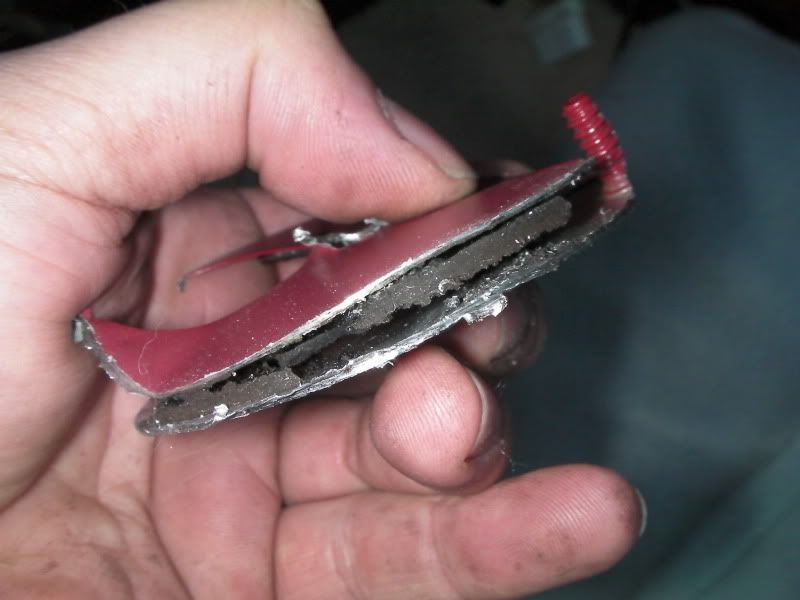
Then a simple trial fit of the grommet and all seems perfect...
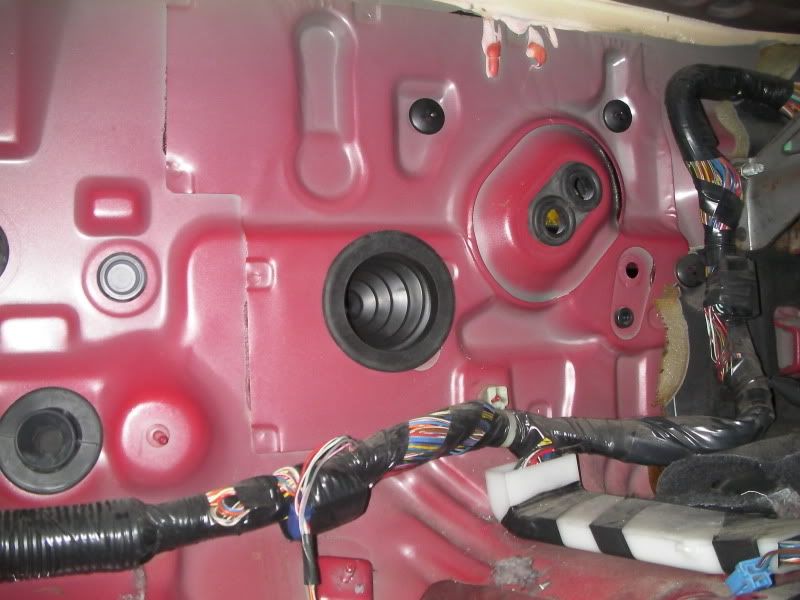
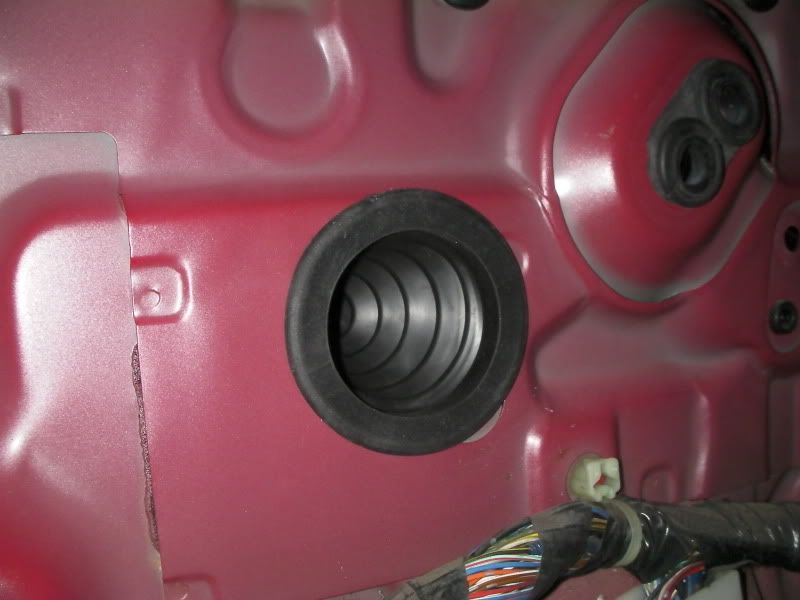
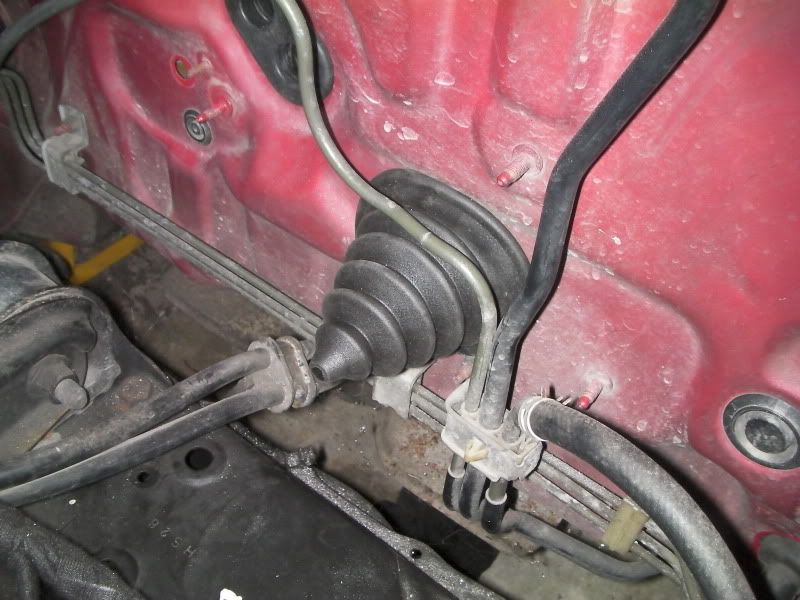
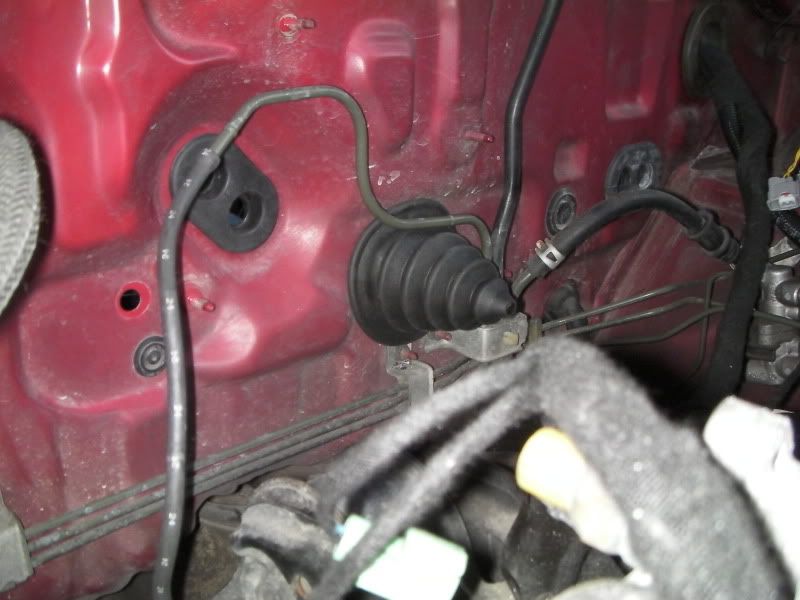
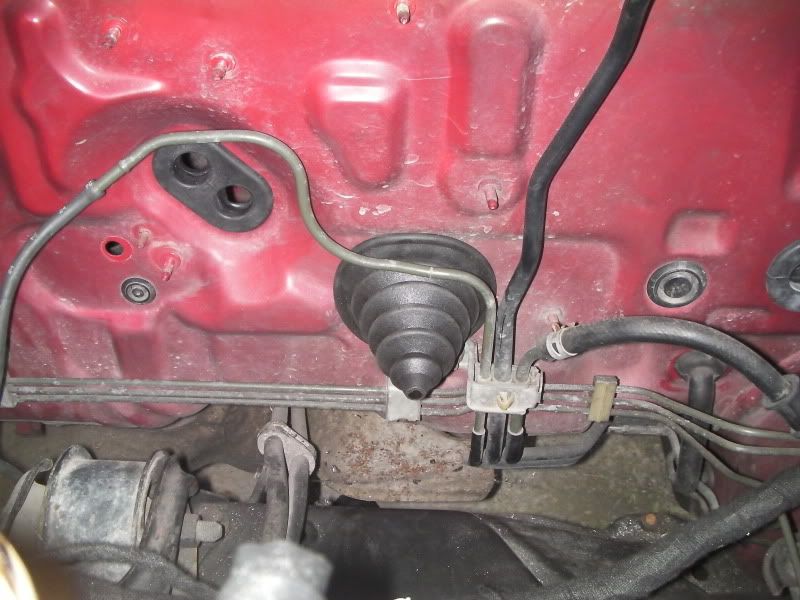
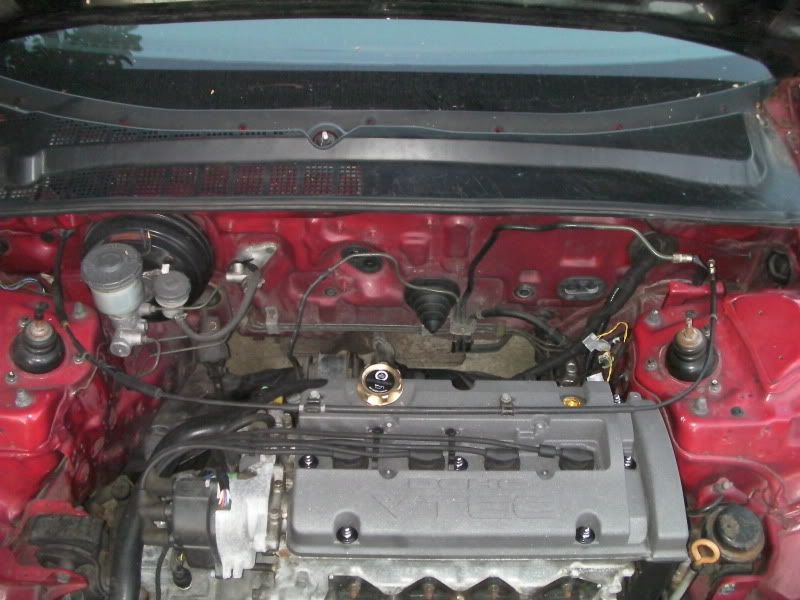
Now once I've painted the bare metal edges of the hole and siliconed the edge to seal the skins, I can go about re-routing the harness and finally finish the wire tuck
